Food safety is a subject that commands the attention of both the general public and health authorities alike. In recent weeks, Palmer Candy Company, a well-known confectionery brand, announced a voluntary recall of some of its popular candy and snack products in 17 states due to a potential salmonella risk. This extensive recall has generated significant concern among consumers, many of whom have enjoyed these sweets for years without incident. In this in-depth report, we will examine the details behind the recall, the nature of salmonella contamination, and the broader implications for both consumers and the food industry. Whether you are a curious consumer, a concerned parent, or a small business owner, understanding how such recalls unfold—and how to respond—can make a real difference in safeguarding public health.
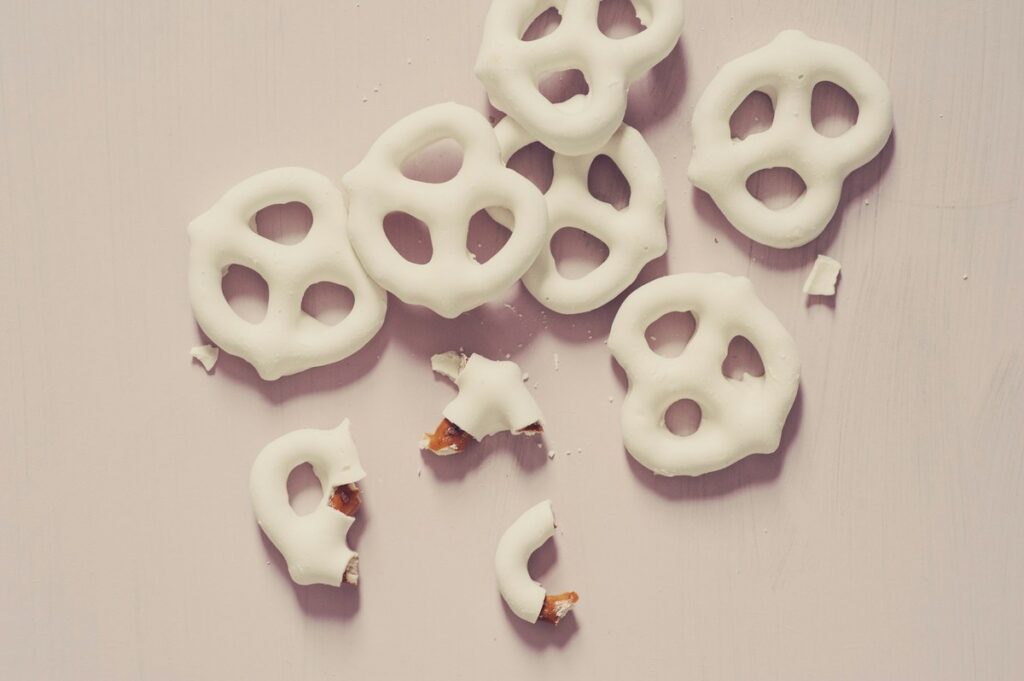
1. Introduction: Why Food Recalls Matter
Food recalls are a serious matter, not only because they disrupt consumer confidence in a product but also because they can pose immediate health risks. When a manufacturer announces a recall due to salmonella, it highlights the gravity of a potential outbreak. Salmonella is not a trivial bacterium: it can cause severe illness, and in some cases, hospitalization or even death, particularly among vulnerable populations such as young children, pregnant women, the elderly, and those with weakened immune systems.
The Palmer Candy Company has been in the confectionery business for years, producing a variety of candies, chocolates, and snacks distributed widely across multiple states. They have a loyal consumer base, many of whom appreciate the taste, affordability, and local heritage associated with the brand. The recent recall is therefore not just about removing products from shelves; it is also about addressing consumer fears, preventing further spread of any contamination, and maintaining the trust that customers have placed in the company.
In this era of global supply chains and instant information, recalls can quickly become headline news. The proliferation of social media and online forums often amplifies concerns, leading to confusion if official information is not readily available. This is why transparent, prompt, and detailed communication from both the company and health authorities—like the U.S. Food and Drug Administration (FDA)—is crucial. The Palmer Candy Company’s recall notice, released through official channels, aimed to provide details on which products are affected, where they were sold, and how consumers should respond.

In the sections that follow, we will delve into multiple facets of this recall. We will start by taking a closer look at the Palmer Candy Company itself, exploring its history and why this recall is particularly significant. Next, we will discuss the precise nature of the contamination risk, focusing on the salmonella bacterium—its origins, how it spreads, and why it is so dangerous. We will then break down the timeline of the recall announcement, identifying which products are implicated and the specific steps the company is taking to remove them from circulation.
From there, we will explore how salmonella contamination is typically discovered and managed, and why certain states—17 in total—were particularly impacted. We will also address the practical steps consumers can take to protect themselves and their families, from checking product codes and expiration dates to properly disposing of or returning the recalled items. Furthermore, we will examine the role of the FDA and other regulatory agencies in enforcing standards and ensuring that companies like Palmer Candy Company handle contamination events responsibly.
Lastly, we will take a broader look at the systemic issues in food safety, drawing lessons from this recall and from past events that have shaped how recalls are managed today. Food safety is a collective responsibility—one shared by manufacturers, distributors, retailers, regulators, and consumers. By understanding how each of these parties interacts and responds during a recall, we can better appreciate the challenges and the strides made in modern food safety protocols.
Whether you are learning about this recall for the first time or seeking a deeper understanding of the situation, this comprehensive exploration aims to clarify the complexities behind a major salmonella-related recall. While no one wants to hear that a beloved candy product might be contaminated, knowledge is power. The more we know about the cause, the response, and the prevention of foodborne illnesses, the better equipped we are to keep ourselves and our communities safe.
2. Palmer Candy Company: A Brief Background
Before diving into the specifics of the recall, it is helpful to understand the Palmer Candy Company and its position within the confectionery industry. Founded decades ago, Palmer Candy is known for producing a wide array of sweet treats, from chocolate-covered snacks to peanut butter confections and seasonal specialty items. Over the years, the company has developed a reputation for quality and affordability, often positioning itself as a family-friendly brand with roots in local communities.
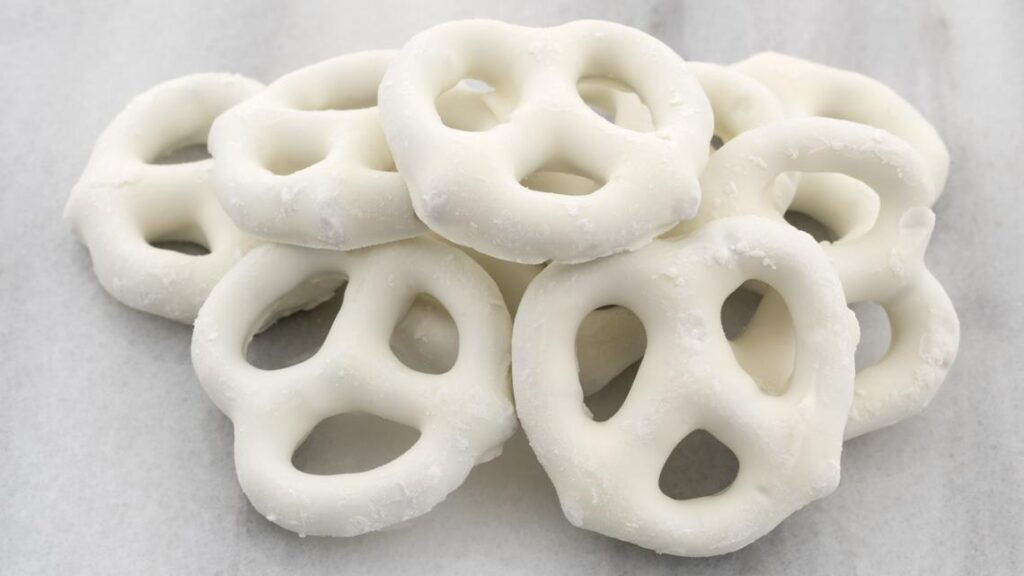
Company Origins
The Palmer Candy Company, like many regional confectioners, started small. Early on, the focus was on simple, classic candies that appealed to a broad range of tastes. Over time, the product line expanded to include chocolate-coated pretzels, peanut clusters, fudge brownies, and other snack items. The brand’s growth was propelled by partnerships with grocery chains and convenience stores, allowing Palmer’s treats to reach more customers across multiple states.
Growth and Distribution
One reason this particular recall is significant is the extensive reach of Palmer Candy’s distribution network. While some candy companies remain local or regional, Palmer Candy has successfully placed its products in national and regional supermarket chains, discount stores, and online marketplaces. This wide distribution network is both a strength—giving the company a broad customer base—and a potential weakness—because if contamination occurs, it can spread quickly and widely.
Product Portfolio
Palmer Candy’s portfolio typically includes:
- Chocolate Bars: Milk chocolate, dark chocolate, and special flavor variations.
- Peanut Butter Snacks: Peanut butter cups, peanut butter clusters, and peanut butter-stuffed pretzels.
- Holiday/Seasonal Items: The company often produces holiday-themed candies, like Valentine’s Day hearts or Easter eggs, which are popular among families.
- Snack Mixes: A combination of nuts, dried fruits, and candy-coated pieces that appeal to customers looking for sweet-and-salty flavors.
The recall is believed to impact multiple products in the peanut butter and snack mix categories, though the official recall notice lists the exact SKUs and lot numbers. Understanding how extensive Palmer Candy’s product line is clarifies why the recall has gained so much attention: many consumers who regularly purchase sweet snacks may unknowingly have these recalled items in their pantries.
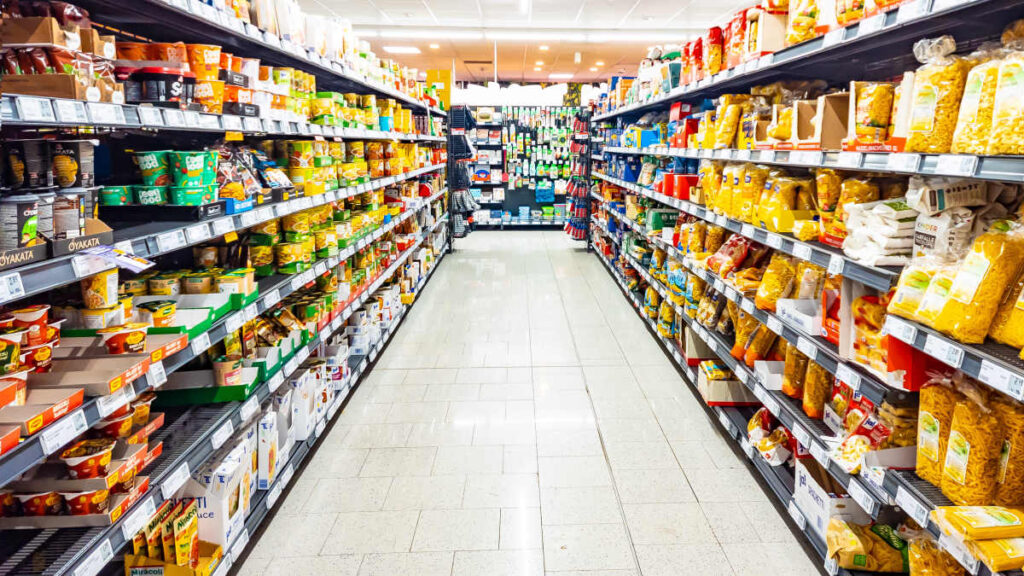
Commitment to Quality (and the Challenge of Recalls)
In company statements and marketing materials, Palmer Candy has long emphasized its commitment to quality ingredients and manufacturing practices. Recalls are never a trivial matter for any company, but they can be especially damaging for a brand that prides itself on consumer trust. Nevertheless, a recall—if handled transparently and proactively—can also demonstrate a company’s dedication to consumer safety. By voluntarily recalling potentially contaminated products, Palmer Candy is showing that it places the health and well-being of its customers above short-term profit.
Past Record of Safety
Until now, the Palmer Candy Company has maintained a relatively clean track record, with few, if any, large-scale recalls or controversies. This new recall due to potential salmonella contamination, therefore, represents a significant event in the company’s history. It may lead to increased scrutiny from both consumers and regulators, who will want to ensure that the root causes of contamination are identified and addressed. The company’s reputation, built over years, now rests on how effectively it manages this crisis.
Balancing Tradition and Modern Food Safety
Many regional confectionery brands like Palmer Candy walk a fine line between preserving traditional manufacturing techniques and adhering to modern food safety standards. Over time, new regulations and technologies have emerged to help detect contaminants like salmonella more rapidly. While tradition is a selling point—think of old-fashioned candy recipes—modern supply chain complexities can introduce new risks. Ingredients might be sourced from multiple suppliers, each of which must maintain rigorous standards. A breakdown at any point can lead to widespread contamination.
The Way Forward
Once the immediate concerns of the recall are addressed, Palmer Candy will likely conduct an internal review to strengthen its safety protocols. This may involve updating manufacturing processes, retraining staff, or investing in more advanced testing equipment. The company’s response to this recall will be pivotal. If handled properly, Palmer Candy can reassert itself as a brand that truly cares about consumer well-being. If handled poorly, it risks damaging a legacy built over decades.
As we proceed through this article, we will explore how the recall was announced, the scientific underpinnings of salmonella contamination, and what steps consumers should take. By keeping the Palmer Candy Company’s background in mind, readers can better appreciate the significance of this event and the complexities involved in addressing a large-scale recall. From small beginnings to a large distribution network, Palmer Candy’s journey mirrors that of many food manufacturers who must balance growth with unwavering attention to safety.
3. The Recall Announcement: Key Details and Timeline
One of the most critical aspects of any recall is the clarity and timeliness of the announcement. When dealing with potential salmonella contamination, every day counts. If tainted products remain on store shelves—or in consumers’ homes—for too long, the risk of an outbreak grows. The Palmer Candy Company’s recall announcement aimed to provide consumers, retailers, and regulators with the essential details needed to minimize harm.
Early Indicators and Internal Testing
Recalls typically begin when either internal testing or external oversight agencies detect a potential problem. In many cases, routine testing on production lines or random product sampling identifies traces of salmonella. Alternatively, a complaint or illness report from a consumer might prompt a more thorough investigation. Although the exact sequence of events for the Palmer Candy recall has not been fully disclosed, it is likely that initial tests flagged a contamination risk in specific product batches, prompting further investigation.
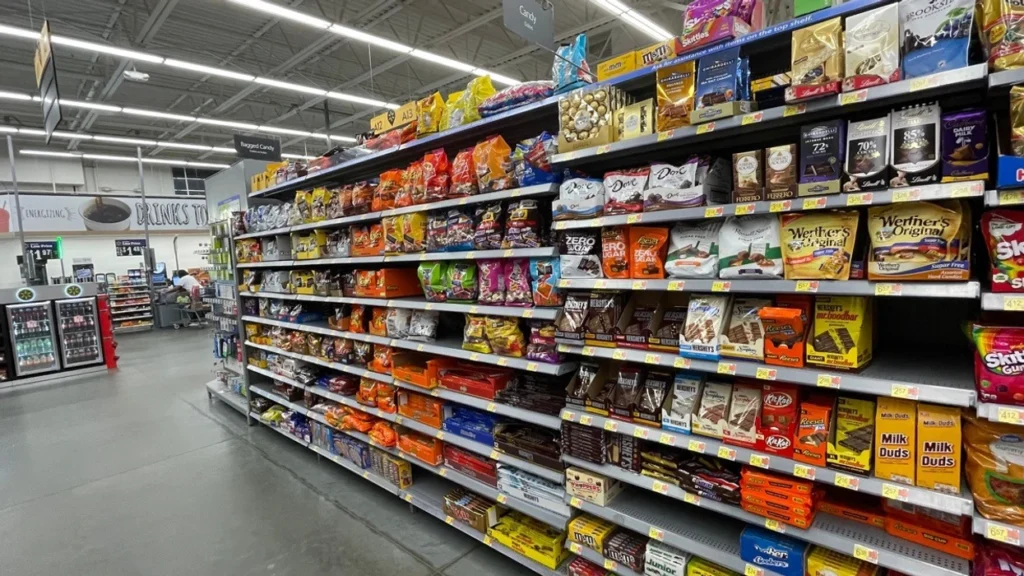
Coordinating with the FDA
Once a company suspects contamination, it is standard procedure to alert the U.S. Food and Drug Administration (FDA) and other relevant state agencies. The FDA plays a central role in evaluating the seriousness of the contamination, overseeing the recall strategy, and disseminating information to the public. In the case of Palmer Candy, the company reportedly worked closely with the FDA to determine the scope of the recall, identify which states were impacted, and develop clear guidelines for consumers.
The Public Announcement
The public announcement was made through multiple channels:
- Official Press Release: Palmer Candy Company likely issued a press release distributed via major newswires. This release would have included the specific product names, SKUs, UPC codes, and “best by” dates to help consumers identify the affected items.
- Company Website: The company’s website typically provides a centralized resource for recall information, including FAQs, contact details for customer service, and instructions on how to return or discard products.
- FDA Recall Notices: The FDA’s website hosts a dedicated section for recalls, market withdrawals, and safety alerts. Once the recall was confirmed, the agency posted the relevant details, often including images of the product packaging to help consumers.
- Social Media and Local News: In today’s digital age, many consumers learn about recalls via social media platforms or local news broadcasts. The immediacy of these outlets can be critical for reaching people who might otherwise miss the official press release.
Specific Products Recalled
While the recall likely encompassed multiple product lines, the main items flagged for potential salmonella contamination typically include peanut butter cups, chocolate-covered peanuts, peanut clusters, and snack mixes containing peanut or chocolate components. Salmonella contamination is often linked to nuts or nut-derived ingredients because peanuts can harbor the bacteria if not processed correctly.
The recall notice presumably listed details such as:
- Product name (e.g., “Chocolate-Covered Peanut Clusters”)
- Package size (e.g., “12 oz bag” or “16 oz canister”)
- UPC codes (the barcode number on the packaging)
- Lot codes or batch numbers
- “Best by” or expiration dates
Such specificity is crucial. Without it, consumers might discard perfectly safe products or, worse, keep unsafe products because they are unsure if they fall under the recall.
Geographic Reach: 17 States
One of the standout points in the recall announcement was the number of states affected—17 in total. This wide reach underscores the brand’s distribution network and raises the stakes for effective communication. For instance, if a single distribution center services multiple states, any contaminated batch can quickly move across state lines. The recall notice usually specifies which states received shipments of the affected products, often naming them directly:
- Alabama
- Arizona
- Colorado
- Georgia
- Illinois
- Indiana
- Iowa
- Kansas
- Michigan
- Minnesota
- Missouri
- Nebraska
- Ohio
- Pennsylvania
- Tennessee
- Texas
- Wisconsin
(Note: This list is illustrative. The actual states involved would be confirmed by the official recall notice.)
Timeline of Events
The timeline is critical for both consumers and regulators:
- Detection: Internal or external tests detect salmonella or “red flags” in a specific product batch.
- Investigation: The company halts production in the suspected area, quarantines the batch, and performs additional testing.
- Regulatory Consultation: The company notifies the FDA and relevant state agencies to discuss the scope of contamination and recall strategy.
- Recall Decision: Once the contamination risk is confirmed, the company opts for a voluntary recall, removing all potentially affected items from store shelves.
- Public Notification: The company and the FDA release details to the media, instructing consumers to return or discard the recalled products.
- Ongoing Testing: Even after the announcement, the company continues testing to ensure no other products are compromised.
- Resolution and Follow-up: The company, possibly in collaboration with the FDA, will issue updates, finalize the recall process, and implement preventive measures to avoid future occurrences.
Consumer Response
The public’s reaction to a recall can vary from alarm to apathy, depending on how well the information is communicated. Some consumers may panic and discard all candy products, while others might not hear about the recall at all. Effective recall announcements aim to reduce confusion by providing step-by-step instructions. For instance, the notice might state:
- “If you purchased [Product Name] with UPC Code 1234567890 and a best-by date between June 1 and July 15, do not consume it. Return it to the retailer for a full refund or dispose of it safely.”
Retailer and Distributor Response
Retailers also play a significant role. Many large supermarket chains have systems to flag recalled items at checkout, preventing sales once the recall is in effect. Store managers might remove the products from shelves and post recall notices near the candy aisles. Distributors who supply smaller mom-and-pop stores also must act quickly, pulling inventory from their networks. This multi-tiered approach ensures that the recalled items are removed from circulation as thoroughly as possible.
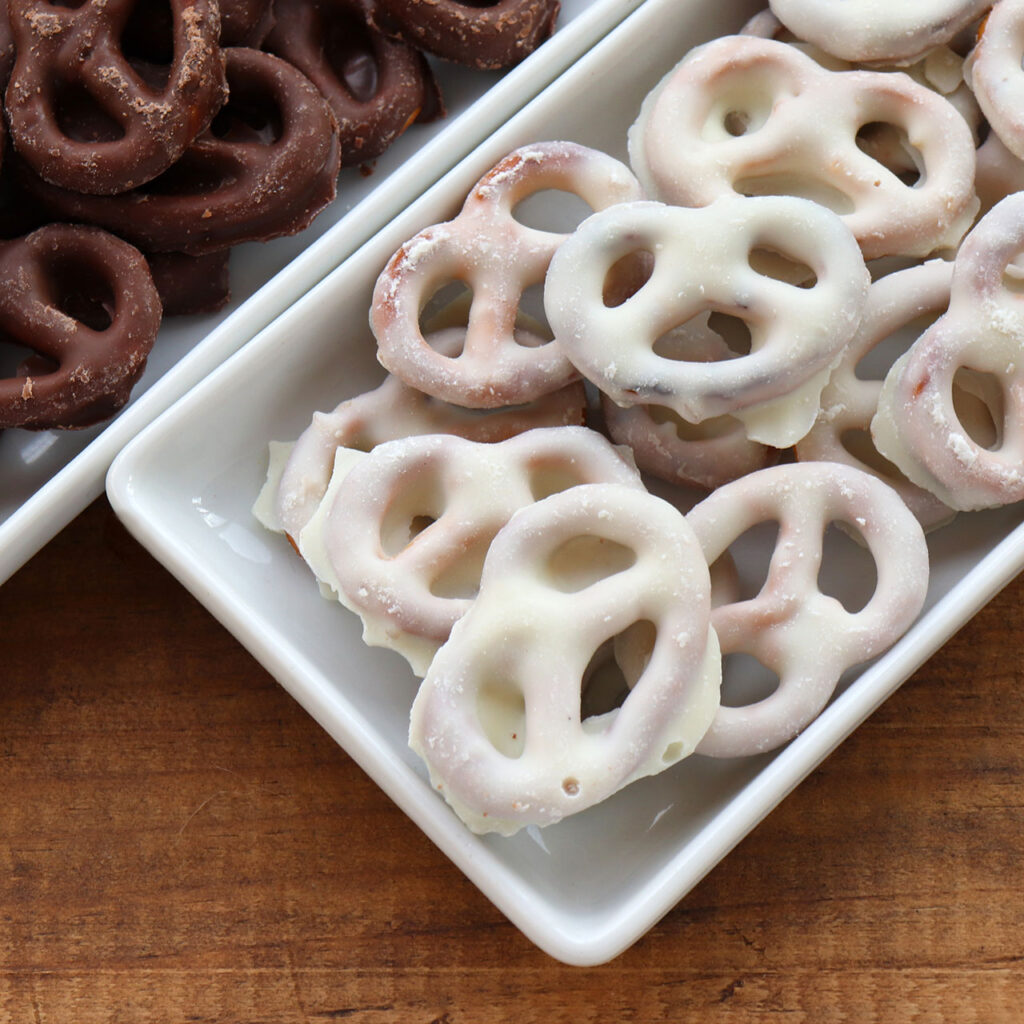
Lessons in Transparency
A well-managed recall is characterized by openness and a willingness to shoulder responsibility. By detailing the nature of the risk (salmonella) and explaining what steps are being taken, Palmer Candy can mitigate damage to its reputation. Companies that attempt to minimize or conceal the scope of a recall often face public backlash, legal repercussions, and a loss of consumer trust. In contrast, a swift and transparent recall can, over time, reaffirm the company’s commitment to safety.
Ongoing Monitoring
Even after the recall is announced, the story does not end. Additional testing and consumer feedback might reveal more affected products or even exonerate certain batches previously suspected. The FDA will continue to monitor the situation, and the company is typically required to submit progress reports until the recall is considered closed. If no illnesses are reported or if reported illnesses remain minimal, the recall can be deemed successful in preventing a broader outbreak.
4. The Scope of the Salmonella Risk
To fully appreciate why the Palmer Candy Company’s recall is such a critical event, one must understand salmonella—what it is, how it spreads, and the serious health risks it poses. Salmonella is one of the most common causes of foodborne illness, resulting in millions of cases globally each year. In the United States alone, the Centers for Disease Control and Prevention (CDC) estimates that salmonella causes about 1.35 million infections, 26,500 hospitalizations, and 420 deaths annually.
What is Salmonella?
Salmonella is a genus of bacteria typically found in the intestines of humans and animals. More than 2,500 serotypes of salmonella exist, but only a subset regularly causes illness in people. Common sources include raw poultry, eggs, unpasteurized milk, and contaminated produce. However, salmonella can also contaminate dry foods like cereals and snacks if sanitary conditions are compromised at any point in the supply chain. This is why the detection of salmonella in candy or peanut butter snacks is particularly alarming: these products are not typically cooked or heated by the consumer before eating, removing a key step that might otherwise kill the bacteria.
Symptoms of Salmonella Infection
People infected with salmonella usually experience symptoms within 6 to 48 hours after ingesting contaminated food. The most common symptoms include:
- Diarrhea (often severe and watery)
- Fever
- Abdominal cramps
- Nausea
- Vomiting
- Headache
- Chills
Most healthy individuals recover within 4 to 7 days without specific treatment, although rest and hydration are crucial. However, in some cases, the diarrhea can be so severe that it leads to dehydration, requiring hospitalization. Certain strains of salmonella can also enter the bloodstream and cause life-threatening infections in other parts of the body, such as the bones, joints, or nervous system.
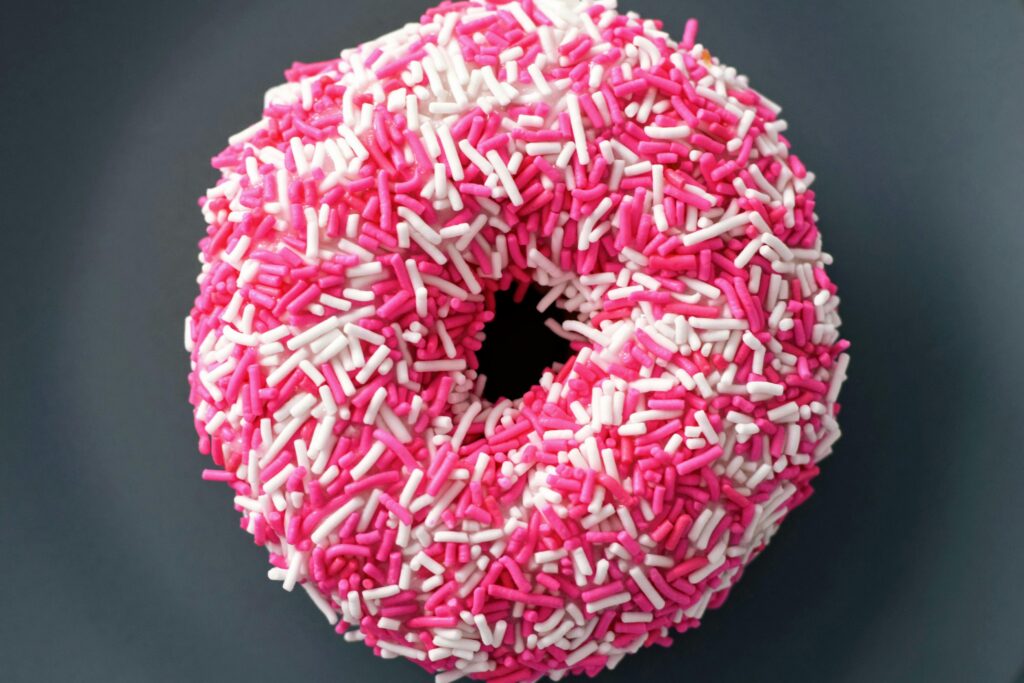
High-Risk Populations
While anyone can contract salmonella, certain groups face a higher risk of severe illness:
- Infants and Young Children: Their immune systems are not fully developed, making them more susceptible to complications.
- Older Adults: With aging, immune function declines, increasing vulnerability.
- Pregnant Women: Salmonella can pose added risks during pregnancy, potentially affecting fetal health.
- Immunocompromised Individuals: Those undergoing chemotherapy, living with HIV, or on immunosuppressive drugs may have reduced defenses against bacterial infections.
How Salmonella Contamination Occurs in Candy
Salmonella contamination in candy or snack products often stems from raw ingredients—such as peanuts—that may harbor the bacteria if not properly processed. For instance, peanuts can be contaminated if they come into contact with animal feces in the field or if they are processed on equipment that was not sanitized correctly. Additionally, post-processing contamination can occur if a fully cooked or otherwise treated product passes through a facility where the environment is not sterile.
Common vectors of contamination include:
- Cross-Contamination: Equipment used for multiple food items without thorough cleaning.
- Infected Workers: Employees who handle the product while carrying salmonella, potentially transferring it to the product.
- Contaminated Water: Water used in cleaning or cooling processes that contains the bacteria.
- Poor Storage Conditions: Salmonella can survive for extended periods on surfaces or in dry foods, which makes thorough cleaning and proper storage essential.
Why Recalls Are Essential
Given how quickly salmonella can spread and how severe the illness can be, recalls are a fundamental tool for consumer protection. Once a company identifies contamination, pulling the product from the market is the most direct way to prevent further cases of illness. Recalls also serve as a signal to other players in the supply chain to review their practices and ensure no additional contamination is present.
The Role of Testing
Manufacturers are encouraged—and often required—to conduct routine microbiological tests on their products. Such tests typically involve sampling finished products or raw ingredients to detect pathogens like salmonella, listeria, and E. coli. However, no testing regime is foolproof, especially when dealing with large volumes of goods. Even a small lapse can lead to widespread contamination if the production line is running continuously and distributing products across multiple states.
Health Consequences and Cost
Beyond the human cost, salmonella outbreaks can be financially devastating. Hospitalizations, medical treatments, and time lost from work are just the beginning. If a consumer falls ill, they might face extended medical bills or even long-term complications. On the corporate side, companies face recall costs, potential lawsuits, regulatory fines, and damage to their brand reputation. The cost to the broader food industry is also significant, as widespread recalls can shake consumer confidence in entire product categories.
Tracking and Tracing
One advancement in the modern food industry is improved traceability. Barcodes, lot numbers, and advanced tracking software help companies and regulators trace a contaminated product back to its source more quickly. This technology was undoubtedly employed in the Palmer Candy recall to pinpoint the exact batches and distribution channels. Without it, the recall might have been even broader, leading to unnecessary waste and confusion.
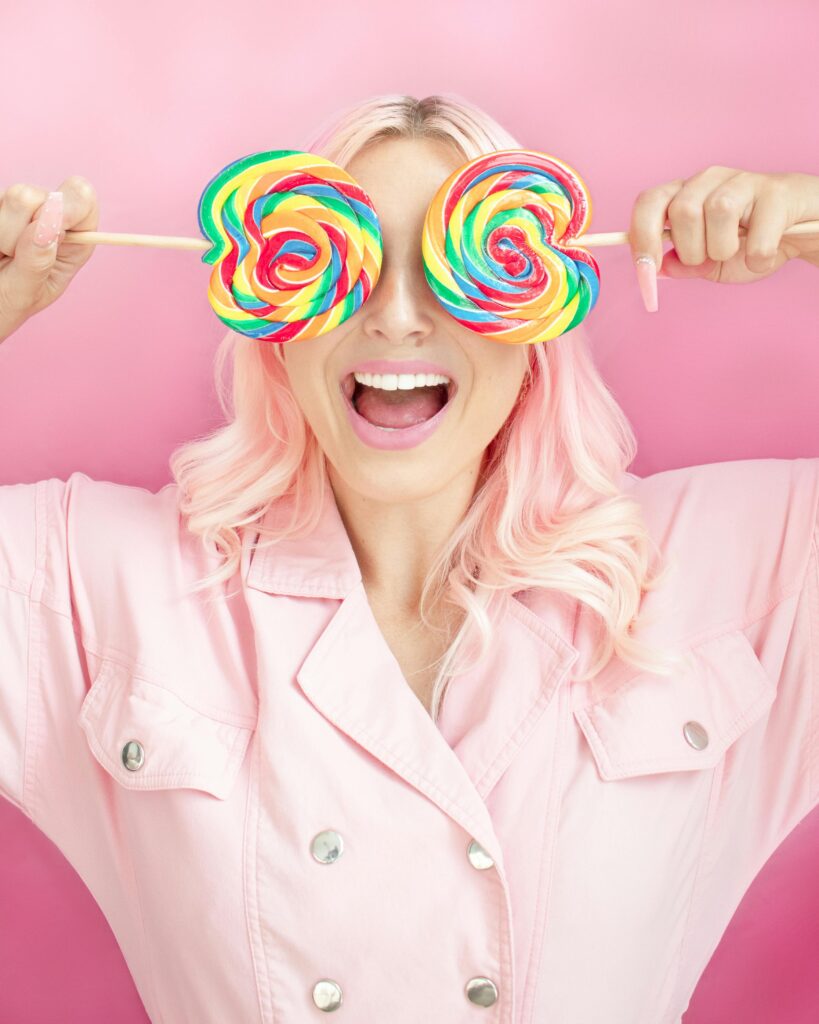
Consumer Vigilance
Consumers also play a role in reducing salmonella risk. Key practices include:
- Proper Handwashing: Washing hands thoroughly with soap and warm water before handling food.
- Checking Recalls: Staying informed about the latest recalls through the FDA website, local news, or social media.
- Proper Storage: Storing candy and snacks in cool, dry places to minimize bacterial growth.
- Heeding Expiration Dates: Although not all bacteria is related to product age, discarding items past their “best by” dates can help maintain product quality.
Looking Ahead
The Palmer Candy Company’s recall highlights the complexities of ensuring food safety in a globalized supply chain. While salmonella contamination can occur in various foods, it often surprises consumers when found in products like candy, which are not typically associated with bacterial risks. However, the presence of peanut butter or nuts in these confections is a clear reminder that no product is entirely immune to contamination if the underlying processes fail at any step.
As consumers, remaining vigilant about recalls, storing products properly, and understanding the basics of foodborne pathogens like salmonella are important steps toward staying safe. For companies, the recall underscores the need for rigorous quality control measures, transparent communication, and swift action when contamination is detected. While no system can be 100% foolproof, every lesson learned from such recalls can push the industry toward safer, more reliable practices.
5. Understanding Salmonella: Origins, Transmission, and Impact
To truly grasp why a salmonella-related recall from a candy company sparks such concern, it is crucial to explore the bacterium’s broader context. Salmonella is not a new threat; it has been a persistent public health challenge for decades. However, changes in global food production, distribution networks, and consumer habits can influence how and where salmonella emerges. By delving into the biology and ecology of salmonella, we can appreciate why it remains such a formidable adversary in the realm of food safety.
A Closer Look at the Bacterium
The salmonella genus encompasses multiple species and thousands of serotypes, but Salmonella enterica is the one most commonly associated with human infections. Within Salmonella enterica, there are serotypes like Enteritidis and Typhimurium, which frequently appear in foodborne outbreaks. These bacteria are rod-shaped, flagellated microorganisms capable of surviving in a variety of environments, including the gastrointestinal tracts of mammals, birds, and reptiles.
Natural Reservoirs
Salmonella naturally resides in the intestines of many animals, often without causing visible illness in the hosts. This asymptomatic carriage allows the bacteria to proliferate in the environment. Livestock such as chickens, turkeys, pigs, and cows can harbor salmonella, passing it on through feces. Consequently, water sources or soils contaminated by animal feces can become vectors for infecting crops, especially produce like lettuce or spinach. When we talk about candy contamination, the path usually involves ingredients like nuts or seeds exposed to contaminated soil or water before being harvested and processed.
Routes of Transmission
Human infection typically occurs via the fecal-oral route, meaning a person ingests food or water that contains salmonella. Some key transmission pathways include:
- Contaminated Ingredients: As in the case of peanut butter or nuts used in candy, if the ingredient itself is contaminated, the final product may carry the bacteria.
- Cross-Contamination: Even if the initial ingredient is safe, contact with contaminated surfaces, equipment, or hands can introduce salmonella.
- Poor Sanitation: Inadequate handwashing by food handlers, unclean utensils, or unmaintained facilities can all contribute to bacterial spread.
- Improper Cooking or Storage: For many foods, thorough cooking kills salmonella. However, candy or snacks that are not cooked by the consumer do not have that protective step.
Environmental Hardiness
One challenging aspect of salmonella is its ability to survive in low-moisture foods for extended periods. Candy, cereal, and other dry snacks can be contaminated at very low moisture levels. The bacteria can remain viable for months or even years, posing a risk long after production. This resilience makes thorough cleaning and consistent monitoring of the production environment vital.
Salmonella’s Global Impact
Salmonella is a leading cause of foodborne illness worldwide, not just in the United States. Developing countries, where refrigeration and sanitation standards might be inconsistent, often see higher rates of salmonella infections. Yet, even in developed nations with strict regulations, outbreaks occur when lapses happen at any point along the food supply chain.
Public Health Burden
While many salmonella infections are self-limiting, the overall burden on public health systems can be substantial. Hospital stays, medical treatments, and the risk of complications in vulnerable groups make it a persistent concern. Moreover, the economic cost includes lost productivity, medical expenses, and the resources spent by health agencies to investigate and manage outbreaks.
Regulation and Surveillance
In the United States, the FDA and CDC collaborate on identifying and controlling salmonella outbreaks. The CDC’s PulseNet system uses DNA fingerprinting of bacteria from infected individuals to detect outbreaks. When multiple people in different regions show genetically similar salmonella strains, investigators suspect a common source. This can lead them to specific brands or production facilities. In the case of a large brand like Palmer Candy, which ships products across state lines, a single contaminated batch can produce illness reports in multiple locations, aiding in the detection of an outbreak.
Role of Food Testing
Routine microbial testing of both raw ingredients and finished products is a core part of modern food safety. However, even robust testing protocols cannot guarantee a 100% salmonella-free product. For instance, if contamination is intermittent or sporadic, random sampling might miss it. That said, the more thorough and frequent the testing, the higher the chance of detecting an issue early, before products reach consumers.
Antibiotic Resistance
A growing concern in the battle against salmonella is the rise of antibiotic-resistant strains. Overuse of antibiotics in agriculture and human medicine can select for resistant bacteria, making infections harder to treat. While this aspect has not been specifically linked to the Palmer Candy recall, it underscores why preventing contamination in the first place is so critical. The fewer people infected, the less risk of encountering antibiotic-resistant strains.
Consumer Awareness and Education
For consumers, knowledge about salmonella can translate into better choices. Though candy might not seem like a high-risk product, recalls like Palmer Candy’s highlight that even unexpected foods can harbor pathogens if supply chain safeguards fail. Practices like checking recall notices, storing snacks properly, and disposing of suspicious products can reduce the risk of infection. Education also extends to how we handle other foods—like raw meats and produce—in the kitchen, limiting cross-contamination and reinforcing the importance of thorough cooking.
The Bigger Picture
Understanding salmonella’s origins and pathways underscores how deeply interconnected our food system is. A single contaminated peanut farm can affect multiple manufacturers if its products are sold to various companies. This interdependency is why industry-wide standards and audits have become more stringent. In the wake of each salmonella outbreak, the FDA often reassesses guidelines, pushing for better traceability, stricter testing, and improved facility design.
Looking Ahead
In the context of the Palmer Candy recall, recognizing the nature of salmonella helps consumers and industry stakeholders alike appreciate the seriousness of the event. Although it is disheartening to discover potential contamination in a familiar brand’s products, the broader lessons can drive innovation and vigilance. By learning from each recall—pinpointing how contamination occurred, addressing it swiftly, and implementing preventive measures—companies can continue to refine their approaches, aiming to make such events increasingly rare.
Salmonella is not going away any time soon. Yet, through science-based policies, industry collaboration, and consumer awareness, we can collectively reduce its impact. As we continue our exploration of the Palmer Candy recall, keep in mind the broader context of salmonella’s biology and ecology. This knowledge forms the backbone of effective responses, ensuring that contamination events are handled with the gravity they deserve.
6. State-by-State Impact: How 17 States Became Involved
One of the most striking details in the Palmer Candy Company recall is that it affected consumers in 17 different states. This widespread impact underscores the complexity of modern distribution networks, where a single production facility can ship goods to numerous regions within days. To understand how a salmonella risk in a candy product can spread so far, it is crucial to examine how distribution channels work, why these particular states were impacted, and what steps local authorities are taking to protect the public.
Distribution Networks Explained
The path a product takes from a factory to a consumer’s home can be surprisingly intricate. Generally, the process involves:
- Manufacturing: Palmer Candy’s primary facility or a contracted manufacturer produces the candy, packages it, and prepares it for shipment.
- Warehousing: Finished goods may be stored temporarily in company-owned or third-party warehouses.
- Wholesale/Distributor Level: Regional distributors purchase or handle large quantities of candy. They might supply supermarkets, convenience stores, and specialty shops.
- Retailers: Stores of all sizes, from national chains to small local grocers, stock the candy on their shelves.
- Online Platforms: In the digital age, products may also be sold through e-commerce websites, which can further extend the geographic reach.
Because each stage can involve multiple players, contamination at the manufacturing level can quickly cascade into multiple states or even countries if the brand has an international footprint.
Why 17 States?
Although the recall specifically mentions 17 states, the actual number can sometimes fluctuate as investigations proceed. The initial count typically reflects states that received confirmed shipments of the affected product batches. If subsequent data shows that a distribution center also sent items to an 18th or 19th state, the recall can expand. For now, these 17 states represent the confirmed distribution channels for the contaminated candy or snacks.
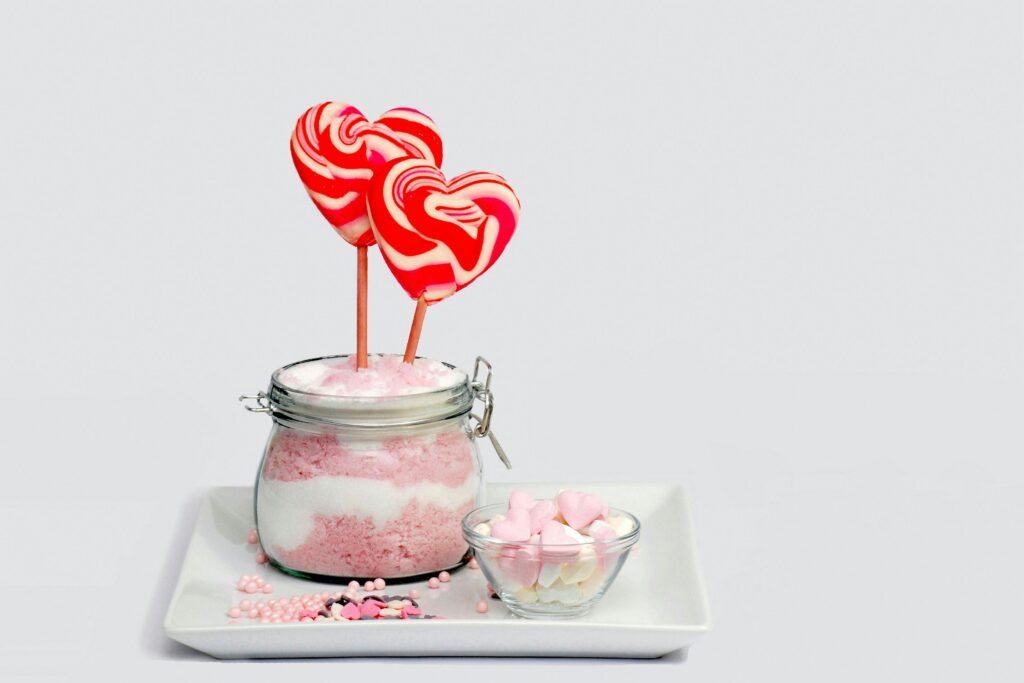
Geographically, these states might be concentrated in one region—like the Midwest or Southeast—depending on where Palmer Candy has historically established strong retail partnerships. Alternatively, the states might be scattered across the country if the brand has a national presence. The distribution list might also reflect the company’s logistic routes. For instance, a large distribution center in Illinois might serve five surrounding states, or a facility in Georgia might supply multiple Southeastern states.
Communication with Local Health Departments
Once the recall is announced, local health departments in each affected state become key players. They often issue their own advisories to local media, providing contact information for consumers who may have questions or concerns. Health departments also monitor hospitals and clinics for any spikes in salmonella-like symptoms that could be linked to the recalled product.
Retailer Notifications
For a recall to be effective, retailers in these 17 states must act quickly. Larger chains typically have computerized inventory systems that can identify recalled SKUs and automatically flag them at checkout, preventing further sales. Smaller independent stores might rely on manual checks, requiring store managers to physically remove items from the shelves. The success of the recall hinges on retailers being both informed and diligent.
Possible Expansion of the Recall
Even though 17 states were listed, there is always the possibility of expansion. Investigations might reveal that a secondary distributor passed the product to a region initially not on the list. Alternatively, consumer reports from outside the identified states might prompt additional scrutiny. The fluid nature of recall investigations makes it critical for all consumers, even those not in the official list of states, to be aware of the situation if they have purchased Palmer Candy products from online platforms or while traveling.
Coordination with the FDA
Throughout this process, the U.S. Food and Drug Administration (FDA) often coordinates with state agriculture and health departments. They might conduct inspections at the production facility, review distribution records, and interview employees. The FDA also supports local agencies in case of an outbreak, providing laboratory services to confirm if any reported salmonella strains match those found in the recalled products.
Consumer Confusion and Misinformation
With so many states involved, confusion can arise. Some consumers may mistakenly assume the recall is national, discarding any candy from the brand without verifying the batch code. Others might be unaware that their specific store was supplied by a distribution center in another state. This underscores why clear, consistent messaging from the brand, retailers, and regulators is essential. Providing state-specific details helps, but the real key is ensuring that consumers know to check the packaging for the exact lot codes or UPCs.
Potential for Illness Reports
If any consumers in these 17 states (or beyond) consume the contaminated product, they might develop salmonella symptoms within days. Public health departments, along with the CDC, can track such illnesses to see if they match the specific strain of salmonella identified in the recall. If a significant cluster of cases emerges in a particular state, that region may receive added attention and resources to contain further spread.
Economic and Reputational Impact
For Palmer Candy Company, having 17 states on the recall list can significantly affect both revenue and brand perception. The cost of retrieving products from shelves, offering refunds, and managing consumer queries can be immense. Meanwhile, the brand’s reputation might take a hit, especially if local news outlets in each state highlight the recall. However, if the company demonstrates transparency and a commitment to rectifying the issue, some of the reputational damage can be mitigated. Consumers often appreciate honesty and swift action, especially if they feel the company is prioritizing their well-being.
State-by-State Variation in Response
Different states might handle recalls with slight variations, depending on their public health infrastructure. Some states might have robust consumer alert systems or more active local media coverage. Others might rely more heavily on the FDA’s national bulletins. In some cases, states with advanced data analytics might be better equipped to detect if any local illness clusters align with the recall.
Looking Forward
While the immediate concern is ensuring that no more contaminated candy remains in circulation, the multi-state nature of the recall also offers a learning opportunity. Palmer Candy, the FDA, and state health departments can analyze how the recall was communicated and how quickly retailers complied. This post-event analysis can inform better recall strategies in the future, making them more efficient and less disruptive.
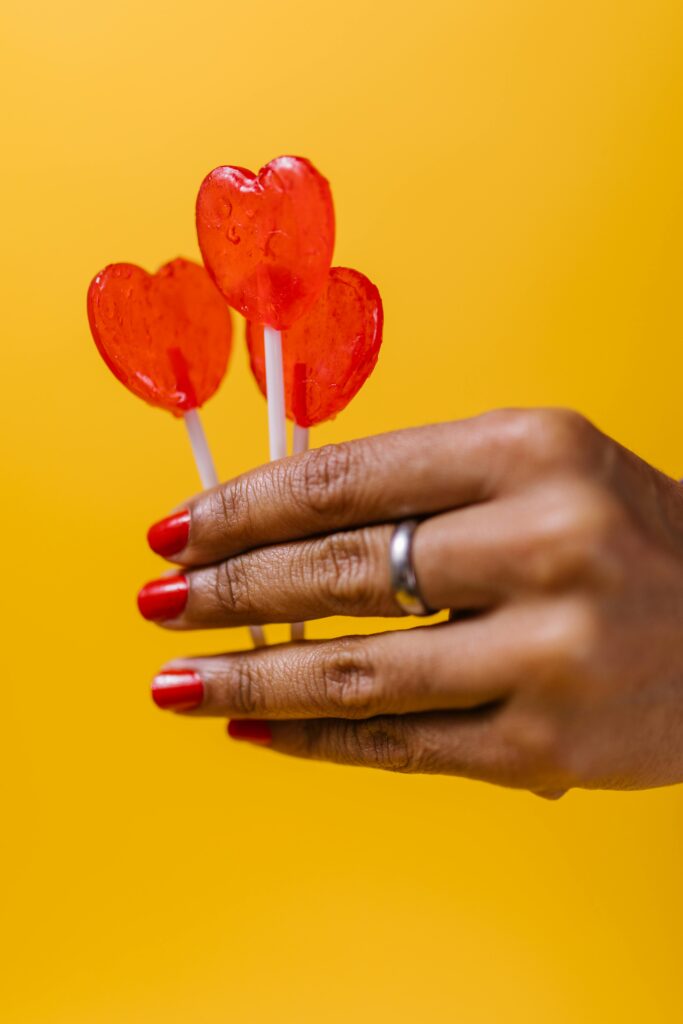
The involvement of 17 states in a single recall highlights how a contamination event in one production facility can have ripple effects across a large geographic area. This underscores the importance of thorough quality control, robust supply chain management, and proactive recall procedures. For consumers, it is a reminder that even beloved regional brands can face unexpected challenges, and staying informed is the best way to remain safe.
7. Consumer Guidance and Best Practices
When a recall as significant as Palmer Candy Company’s salmonella-related event takes place, consumers often find themselves asking: “What do I do next?” It can be stressful to realize that a favorite candy or snack might pose a health risk. However, by following a few key guidelines, individuals and families can minimize their exposure and help ensure that recalled products are removed from circulation effectively. This section outlines the essential steps consumers should take if they suspect they have purchased a recalled product and offers broader tips for preventing salmonella infection in the kitchen and beyond.
1. Identify the Recalled Product
Check Your Pantry: The first step is to verify whether the candy or snack you have matches the product codes listed in the recall notice. This often includes details like:
- Product name (e.g., “Palmer Peanut Butter Clusters”)
- UPC code (found below the barcode)
- Lot number or batch code (usually stamped on the packaging)
- “Best by” or expiration date range
If your package matches the recalled item’s description, do not consume it. If you have already consumed some of it, monitor your health for any signs of salmonella infection.
2. Dispose or Return the Product Safely
If you confirm that your candy or snack is part of the recall, follow the instructions provided by the company or the retailer. Typically, you can:
- Dispose of It: Seal the product in a plastic bag and discard it to prevent anyone else from eating it.
- Return It to the Store: Some retailers offer refunds or replacements. Call ahead or check their website to see if they are participating in the recall.
- Contact Customer Service: Palmer Candy’s recall notice may provide a toll-free number or email for further questions. They can guide you on refunds or replacements.
3. Practice Safe Handling
Even if you choose to dispose of the recalled product, take steps to avoid contaminating your kitchen surfaces:
- Wash Your Hands: Use warm water and soap for at least 20 seconds after handling the product or its packaging.
- Clean Surfaces: Disinfect countertops, utensils, and any other items that might have come into contact with the recalled candy. Use a household cleaning product that kills bacteria, or a solution of bleach and water.
4. Monitor Health Symptoms
If you or anyone in your household consumed the recalled product, stay alert for symptoms of salmonella, such as fever, diarrhea, and abdominal cramps. While many cases resolve on their own, severe symptoms may require medical attention. If you experience persistent vomiting, high fever, or signs of dehydration, contact a healthcare professional promptly. Inform them that you may have consumed a recalled product to help them diagnose and treat your condition more effectively.
5. Communicate with Family and Friends
Not everyone regularly checks recall notices, so a neighbor or family member might still be unaware. If you know someone who frequently buys Palmer Candy products, consider passing along the information. Word-of-mouth can be an effective way to ensure that recalled items are removed from households before anyone falls ill.
6. Maintain Food Safety in General
Recalls can serve as a reminder of broader food safety practices. While the focus here is on candy, salmonella can appear in many foods. Some general tips include:
- Proper Cooking: Thoroughly cook poultry, eggs, and meats to the recommended internal temperatures.
- Avoid Cross-Contamination: Use separate cutting boards for raw meats and other foods. Wash utensils and surfaces after contact with raw ingredients.
- Store Foods Correctly: Keep perishable items refrigerated at or below 40°F (4°C).
- Wash Produce: Rinse fresh fruits and vegetables under running water, even those with inedible skins.
- Hand Hygiene: Regularly wash hands, especially before cooking or eating.
7. Stay Informed About Recalls
Food recalls happen more often than many realize. To stay informed:
- Sign Up for Alerts: The FDA and USDA allow consumers to subscribe to email or text alerts for recalls.
- Check Websites: Periodically visit the FDA’s recall page or your state’s health department website.
- Follow Local News: Many local news outlets quickly report on recalls, especially if they affect widely consumed products.
8. Understand Refund and Liability Policies
Many retailers have policies that allow customers to return recalled products for a full refund, even without a receipt. Palmer Candy’s official recall notice should clarify whether a receipt is required. In some cases, the company might directly handle refunds or replacements if you purchased the item online.
9. Keep Track of Symptoms and Receipts
If you suspect you have fallen ill due to the recalled product, it may help to document your symptoms, the time of consumption, and any medical care received. While many individuals recover without complications, those who require medical attention might have grounds to seek compensation for medical costs. However, such cases often require proof of purchase and medical documentation tying the illness to the recalled item.
10. Use Recalls as a Teaching Moment
If you have children, a recall can be a teaching opportunity. Explain why the candy is being thrown away or returned and what “salmonella” means. Emphasizing the importance of hygiene, handwashing, and careful handling of food can instill habits that protect them in the future.
11. Balanced Perspective
While it is essential to take recalls seriously, it is also helpful to keep them in perspective. Food manufacturers are generally committed to safety and have systems in place to detect issues. Recalls demonstrate that these systems can work, identifying risks before they cause widespread harm. Maintaining trust in the food supply is about acknowledging that mistakes happen but also recognizing that the response mechanism—if transparent and prompt—protects the public.
12. Resources for More Information
- FDA Website (fda.gov/recalls): Comprehensive list of current and past recalls, along with detailed instructions.
- Palmer Candy Company Website: Likely has a dedicated recall page, including FAQs and contact information.
- Centers for Disease Control and Prevention (cdc.gov): Provides resources on salmonella, including symptom checkers and prevention tips.
By following these guidelines, consumers can navigate the recall process with greater confidence. Although discovering that a favorite snack might be contaminated is unsettling, the steps outlined above aim to minimize risk and ensure a swift resolution. With proactive measures and informed decision-making, individuals can protect themselves and their loved ones, reinforcing the importance of vigilance and collective responsibility in food safety.
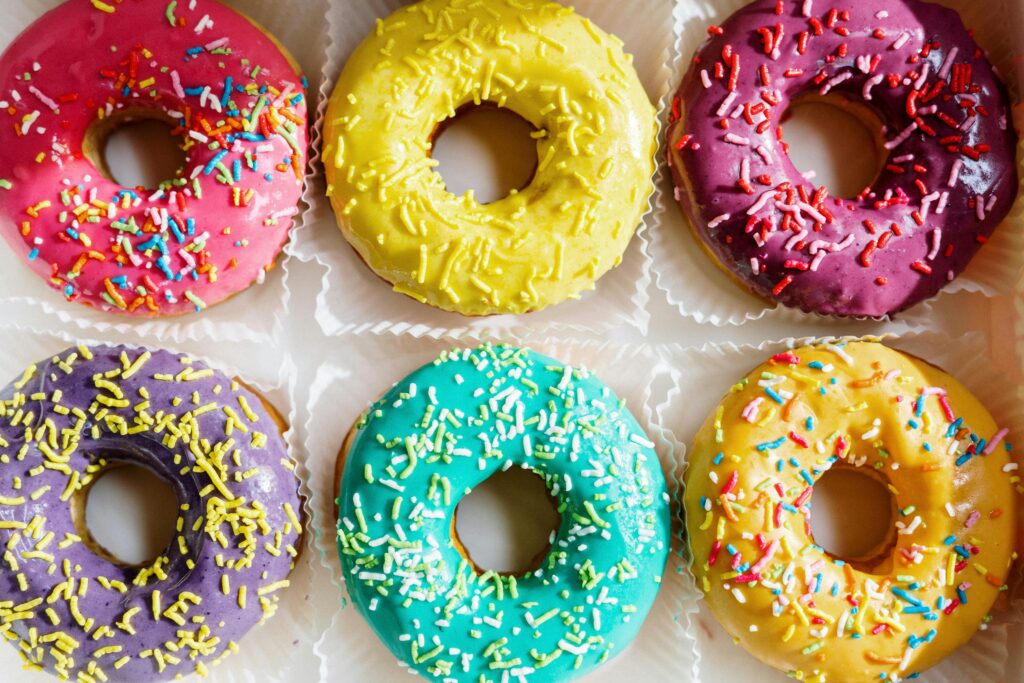
8. The FDA and Food Safety Protocols
When it comes to large-scale recalls like the Palmer Candy Company event, the U.S. Food and Drug Administration (FDA) often plays a pivotal role. This federal agency is responsible for protecting public health by overseeing the safety and security of many of the nation’s food supply chains, as well as drugs, medical devices, and cosmetics. Understanding the FDA’s role—and how food safety protocols are enforced—can shed light on the processes behind recalls and how they aim to prevent harmful outbreaks like salmonella from escalating.
FDA’s Mandate and Authority
Established in 1906 under the Federal Food and Drugs Act, the FDA’s mandate has evolved over time. Today, the agency works under the Food Safety Modernization Act (FSMA) and other regulations to:
- Ensure the safety of most foods (excluding meat, poultry, and some egg products, which fall under the USDA).
- Conduct inspections of domestic and foreign food facilities.
- Oversee labeling and packaging standards.
- Monitor and respond to foodborne illness outbreaks.
- Enforce recalls, either voluntarily initiated by companies or mandated in extreme cases.
Preventive Controls Under FSMA
The Food Safety Modernization Act (FSMA), signed into law in 2011, shifted the focus of the FDA from responding to contamination to preventing it. The law introduced new preventive controls, requiring food facilities to evaluate hazards, implement and monitor effective measures to prevent contamination, and develop corrective action plans. For a candy manufacturer like Palmer Candy, FSMA means they should have a hazard analysis and critical control points (HACCP)-like plan, focusing on areas where salmonella or other pathogens could enter the production line.
The Inspection Process
Food facilities are subject to routine or targeted inspections by the FDA. During these inspections, investigators check for compliance with hygiene standards, record-keeping, and the facility’s adherence to its own preventive control plans. If the FDA finds violations—like unsanitary conditions, poor temperature control, or substandard equipment maintenance—it can issue warning letters or take further enforcement actions. Although the recall might have been triggered by internal testing, the FDA’s subsequent involvement ensures that the entire process is transparent and that corrective measures are implemented.
Traceability Requirements
Traceability is crucial when a recall spans multiple states. Under FSMA, manufacturers and distributors must keep detailed records of their supply chain, enabling the FDA to trace contaminated products back to their source quickly. This system helps isolate affected batches, minimizing the disruption and preventing further distribution. For the Palmer Candy recall, traceability records would detail which states received shipments, the batch numbers, and the dates of distribution.
Voluntary vs. Mandatory Recalls
The majority of recalls in the United States, including the Palmer Candy event, are voluntary. This does not mean the company acts entirely on its own. Rather, it works in cooperation with the FDA, which can provide guidance and oversight. In rare instances where a company refuses to issue a recall despite known risks, the FDA has the authority to mandate one. This power, granted under FSMA, ensures that public safety can be protected even if a company is uncooperative.
Role of Laboratory Testing
The FDA operates laboratories across the country where experts analyze product samples, swabs from production facilities, and other evidence collected during investigations. If a test confirms salmonella in a product that matches the strain found in ill patients, the FDA has solid grounds to support a recall. Conversely, if initial tests are inconclusive, the FDA may ask for repeated sampling or collaborate with the CDC to match bacterial strains from reported illness clusters.
Public Communication
The FDA is responsible for informing the public about significant recalls. Once a recall is classified (e.g., Class I, II, or III, depending on the health risk), the FDA posts it on its website and may also release a news alert. In Class I recalls, where there is a reasonable probability that the product will cause serious health consequences, the FDA emphasizes widespread communication. Salmonella contamination often leads to a Class I recall, given the potential for severe illness.
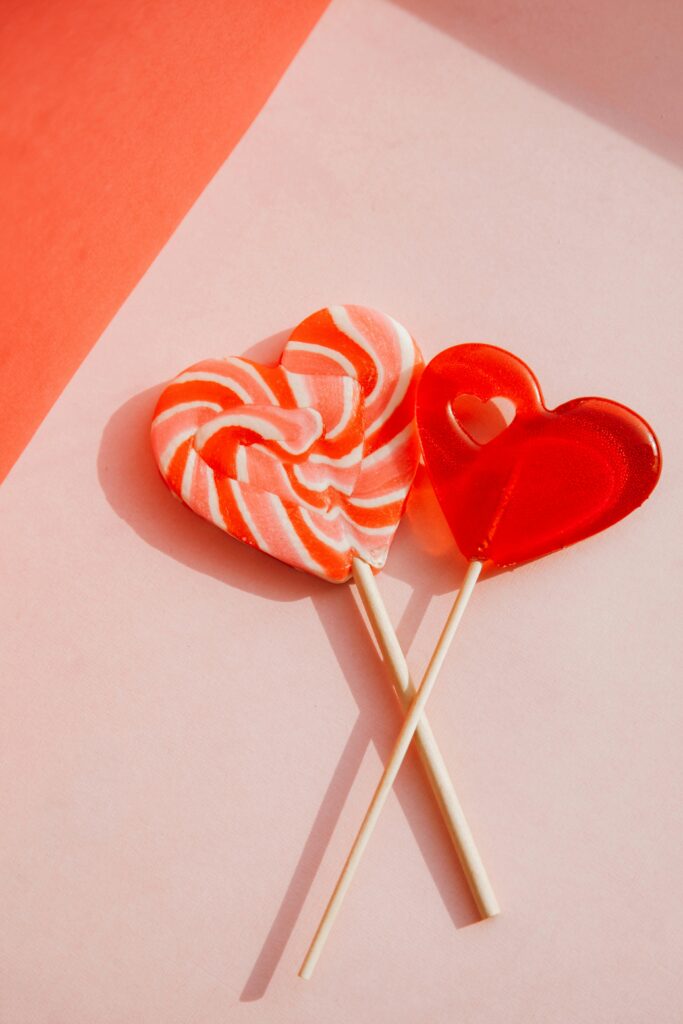
Post-Recall Follow-Up
Once the recall is announced, the FDA continues to monitor the situation. It might:
- Review the company’s corrective actions: ensuring that the root cause of contamination is addressed, whether that involves facility upgrades, new sanitation protocols, or staff retraining.
- Conduct additional inspections: to confirm that the facility now meets safety standards.
- Analyze consumer complaints: verifying if any new cases of salmonella match the recalled products.
- Coordinate with other agencies: The FDA may work alongside the USDA, state agriculture departments, or the CDC if the outbreak crosses into other regulatory jurisdictions or if multiple pathogens are involved.
The Importance of Collaboration
Food safety is a collaborative effort. While the FDA provides national oversight, state health departments often have boots-on-the-ground knowledge of local distribution channels and consumer trends. The CDC assists with outbreak investigation and public health data. Together, these entities create a safety net designed to catch contamination events before they become large-scale crises.
Industry Response
Recalls often prompt changes in industry practices. Competing brands may re-examine their processes, ensuring that a similar contamination does not occur in their facilities. Industry associations might publish updated guidelines, share best practices, or offer training to smaller companies. In the aftermath of a salmonella outbreak, the entire sector can evolve toward stricter standards, thereby enhancing consumer safety overall.
Consumer Empowerment
For consumers, understanding the FDA’s role can boost confidence in the recall process. The presence of a strong regulatory body means that issues like the Palmer Candy recall are met with professional scrutiny and structured interventions. Still, the FDA relies on consumers to report potential problems—like noticing an off smell or taste in a product—and on companies to maintain rigorous internal checks.
The Way Forward
As technology advances, the FDA is adopting more sophisticated tools—such as whole genome sequencing—to identify pathogens and link them to specific outbreaks. Enhanced data analytics can spot trends in real time, reducing the delay between contamination and recall. If Palmer Candy invests in these newer technologies, it might detect contamination earlier in the future, limiting the scale of any subsequent recalls.
Ultimately, the synergy between the FDA’s regulations, company compliance, and consumer vigilance forms the backbone of the U.S. food safety system. While no system is perfect, the recall mechanism—supported by science-based protocols and robust enforcement—ensures that contaminated products are swiftly removed from circulation. By cooperating with the FDA, Palmer Candy can not only address the immediate salmonella risk but also emerge with stronger preventive measures, reassuring consumers of its commitment to their health.
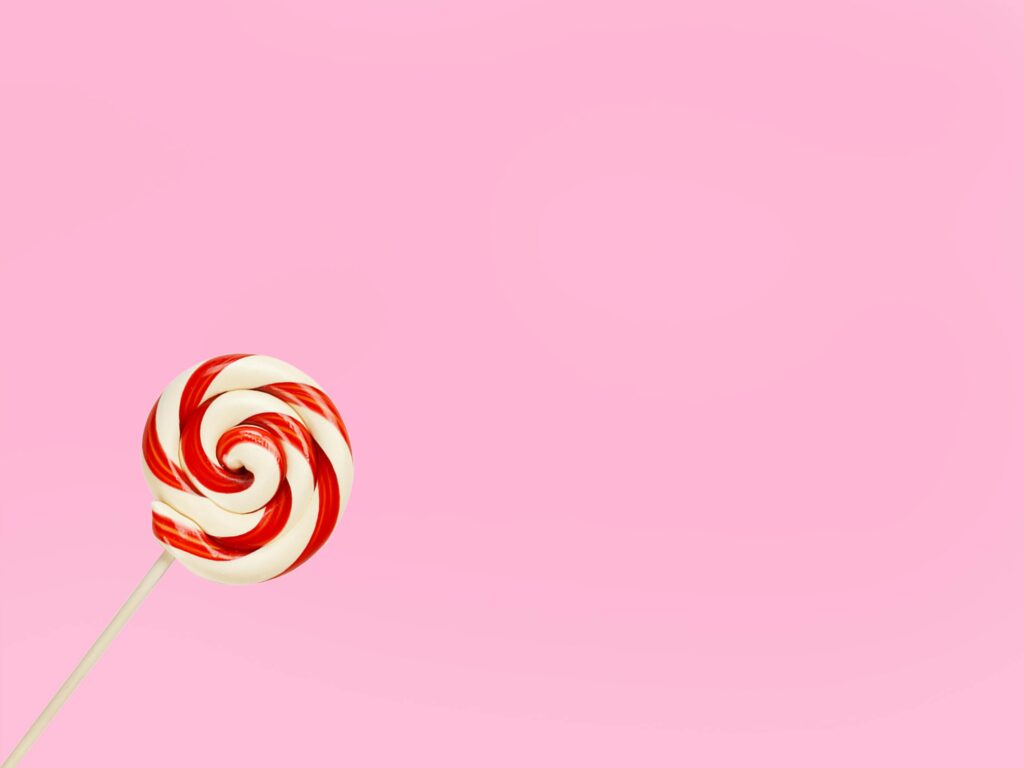
9. Lessons from Past Outbreaks: Building a Safer Future
The Palmer Candy Company recall is not an isolated incident. Over the years, the United States has witnessed several high-profile salmonella outbreaks, each leaving a mark on the collective memory of consumers and shaping the policies of the food industry. By examining past outbreaks, we can identify patterns, glean lessons, and understand how the industry has adapted over time. These insights can help manufacturers, regulators, and consumers build a safer future—one where large-scale recalls become increasingly rare.
The Peanut Corporation of America Scandal (2008-2009)
One of the most notorious salmonella outbreaks in recent history involved the Peanut Corporation of America (PCA). Tainted peanut butter and peanut paste from PCA’s Georgia plant were linked to hundreds of illnesses and several deaths. This incident is widely cited as a catalyst for the Food Safety Modernization Act (FSMA). The scandal revealed serious lapses in PCA’s safety culture, with management allegedly ignoring positive salmonella test results. In the aftermath, regulators and lawmakers recognized the need for stronger preventive controls and better traceability.
Lesson Learned: Corporate responsibility is paramount. If a company fails to uphold basic safety standards, it can jeopardize not only its own existence but also the health of countless consumers and the reputation of an entire product category.
Egg Outbreaks (2010)
In 2010, a major recall involved more than half a billion eggs from two Iowa farms due to salmonella contamination. Investigators found unsanitary conditions and poor biosecurity measures, allowing rodents and other pests to thrive. This outbreak emphasized the importance of facility cleanliness, pest control, and strict adherence to guidelines for egg production.
Lesson Learned: Even in large-scale operations, small oversights—like failing to seal a gap in a wall—can lead to catastrophic contamination. Routine inspections and swift corrective actions are crucial.
Foster Farms Salmonella Outbreak (2013-2014)
Foster Farms, a large poultry producer, experienced a prolonged outbreak that sickened over 600 people across 29 states. Investigations revealed multiple salmonella strains, and the outbreak lasted more than a year. While the company implemented corrective measures, critics argued the response was too slow. This case highlighted how persistent salmonella can be in poultry plants and the challenges in eradicating it entirely.
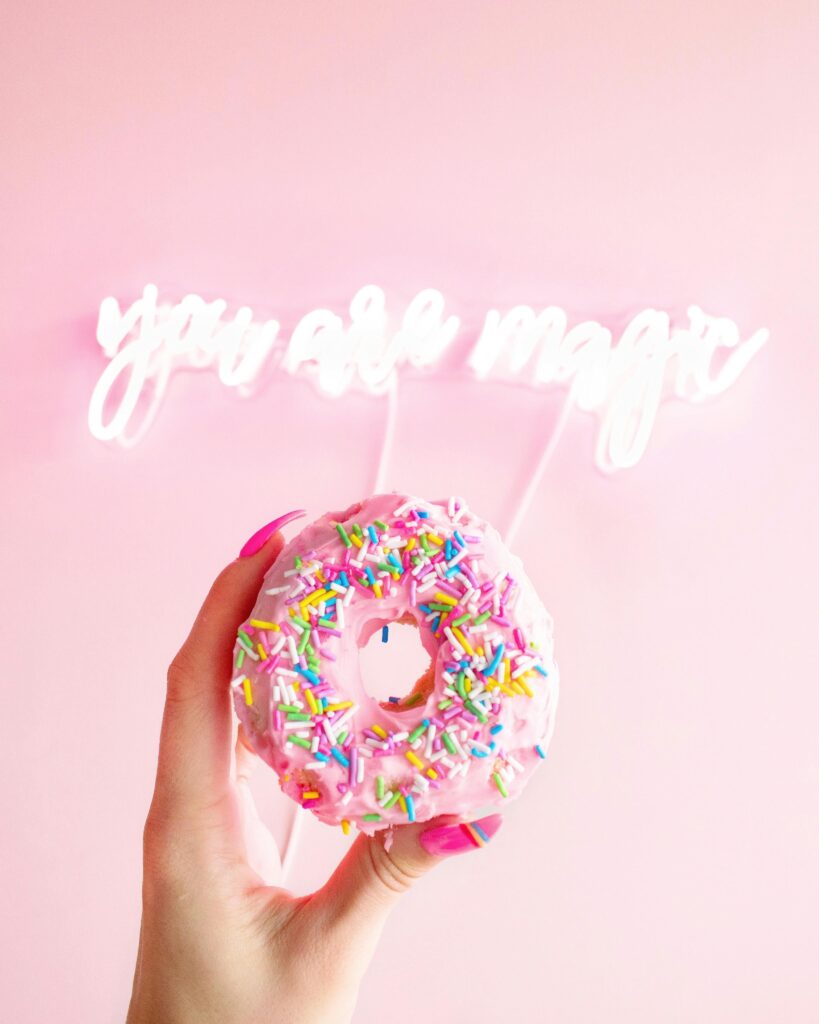
Lesson Learned: The complexities of salmonella control in animal-derived foods underscore the need for multi-layered strategies—improved on-farm practices, thorough cooking, and continuous facility monitoring.
Cucumber Outbreak (2015)
In 2015, contaminated cucumbers imported from Mexico were linked to hundreds of salmonella infections and several deaths. The outbreak drew attention to cross-border supply chain vulnerabilities. Regulatory bodies on both sides of the border faced challenges in pinpointing the source, demonstrating how global trade complicates traceability.
Lesson Learned: International cooperation and robust traceability systems are essential when ingredients or final products cross multiple national borders. Harmonized safety standards and swift information sharing can reduce outbreak durations.
Peanut Butter Cookie Dough Recall (2021)
A lesser-known recall occurred in 2021 when a brand of peanut butter cookie dough tested positive for salmonella. Though it did not result in a large outbreak, it served as a cautionary tale that even ready-to-bake or raw dough products can harbor pathogens if not handled properly during manufacturing.
Lesson Learned: Salmonella can appear in unexpected places, and companies must remain vigilant even when dealing with products that consumers might assume are safe to eat “as is.”
Similarities with the Palmer Candy Recall
The Palmer Candy event bears similarities to these past incidents, especially those involving peanut butter or peanut-derived ingredients. In many cases, the root cause can be traced to inadequate sanitation, cross-contamination, or overlooked red flags in testing data. Each outbreak or recall underscores that no single measure can guarantee absolute safety. Instead, an integrated approach—encompassing strong corporate ethics, rigorous testing, robust regulatory oversight, and consumer awareness—is needed.
How the Industry Has Evolved
In the wake of repeated salmonella incidents, the food industry has adapted by:
- Enhancing Testing Protocols: More frequent sampling, advanced genetic tests, and stricter internal audits.
- Investing in Traceability: Better record-keeping and digital tracking tools help isolate contaminated products swiftly.
- Strengthening Facility Design: Upgraded plants with improved ventilation, pest control, and separate zones for raw vs. cooked products.
- Implementing Third-Party Audits: Many retailers now require suppliers to pass certifications like Safe Quality Food (SQF) or British Retail Consortium (BRC).
- Increasing Transparency: Publicly disclosing test results, forging closer ties with regulators, and swiftly announcing recalls to preserve consumer trust.
Regulatory Changes
The FDA, armed with the FSMA, has greater authority to mandate recalls and enforce preventive measures. Food facilities must develop hazard analysis and risk-based preventive controls (HARPC), a step beyond the traditional HACCP approach. This shift from reactive to preventive strategies aims to minimize the chance of contamination events like salmonella infiltration.
The Role of Consumers
Amid these changes, consumers remain a vital part of the food safety equation. By staying informed through recall alerts, practicing safe food handling, and reporting any suspicious products or illnesses, they help form the final safety net. Grassroots awareness campaigns and social media can rapidly disseminate recall information, reducing the time contaminated products remain on shelves or in homes.
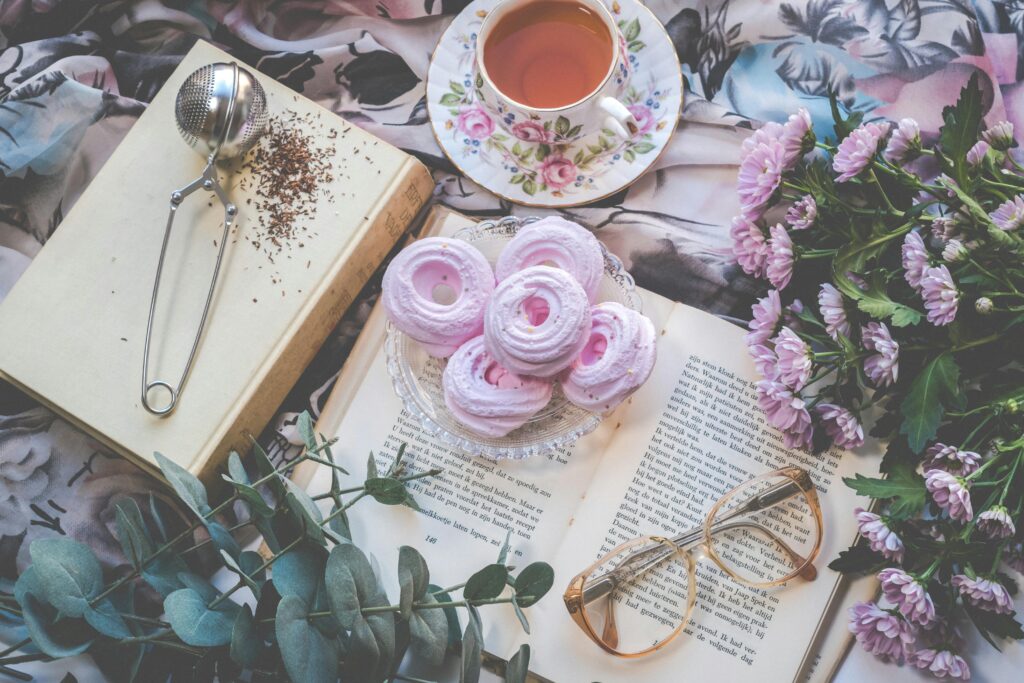
Implications for Palmer Candy
For Palmer Candy, learning from past outbreaks could shape how the company addresses the current recall. It might:
- Reassess its supply chain: Ensuring peanut or nut suppliers meet stringent standards and hold recognized certifications.
- Refine sanitation protocols: Upgrading cleaning schedules, investing in better equipment, and retraining staff.
- Boost transparency: Publicly sharing progress updates on the recall and any corrective measures taken.
- Expand testing: Incorporating more frequent or advanced microbiological tests, especially for high-risk ingredients.
Long-Term Vision
While each salmonella outbreak or recall is undeniably disruptive, they collectively push the industry toward safer standards. Companies that adapt, invest in cutting-edge technology, and maintain open lines of communication with regulators and the public can turn such crises into catalysts for improvement. Over time, the cumulative effect of these lessons can reduce the frequency and severity of foodborne illness outbreaks.
Conclusion: Embracing Continuous Improvement
The history of salmonella outbreaks shows that mistakes happen, but it also highlights the power of collective learning. Each incident, from the Peanut Corporation of America scandal to the cucumber outbreak, has contributed to stronger regulations, better technology, and more vigilant consumer behavior. Palmer Candy’s recall, while unfortunate, is part of this broader tapestry. By adopting best practices gleaned from past events, the company—and the industry at large—can continue to evolve. The ultimate goal is a food system where salmonella recalls become exceedingly rare, and consumer confidence in the safety of everyday products remains high.
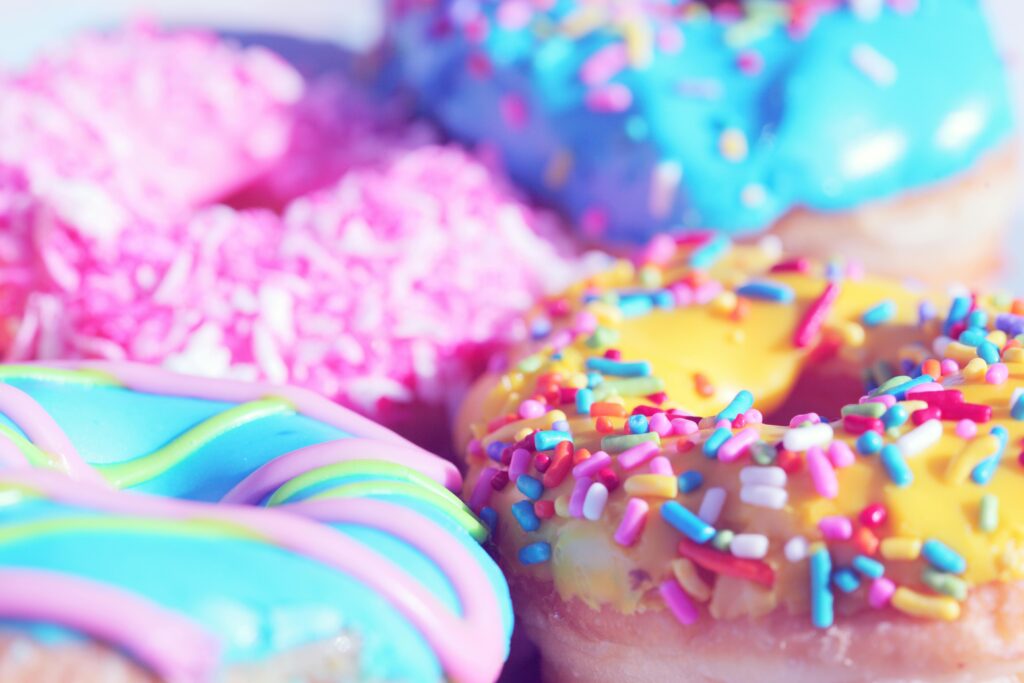
10. Conclusion and Future Outlook
The Palmer Candy Company recall, spanning 17 states and rooted in a salmonella risk, stands as a stark reminder that even beloved confectionery brands are not immune to contamination challenges. This comprehensive exploration has covered the background of Palmer Candy, the recall details, the science of salmonella, and the intricate distribution networks that allowed the affected products to reach multiple regions. We have also delved into the role of the FDA, examined best practices for consumer safety, and reflected on lessons from past outbreaks.
Key Takeaways
- Food Safety is a Collective Responsibility: Manufacturers, regulators, retailers, and consumers all have roles to play. From robust testing and transparent recalls to consumer vigilance in checking packaging and storing products properly, each link in the chain helps safeguard public health.
- Transparency Builds Trust: The success of any recall hinges on clear, timely, and honest communication. By publicly listing affected products, UPC codes, and best-by dates, Palmer Candy and the FDA can minimize confusion and facilitate swift removal of contaminated items from circulation.
- Salmonella’s Persistence: The bacterium’s ability to survive in dry foods, like peanuts or candy coatings, makes it a formidable threat. Strict sanitation, cross-contamination controls, and frequent testing are essential strategies for reducing salmonella risks in the production environment.
- Learning from Past Incidents: Each outbreak or recall, from peanut butter scandals to produce contamination, has shaped modern food safety regulations. Tools like the Food Safety Modernization Act (FSMA) have shifted the focus from reactive measures to preventive controls, emphasizing hazard analysis and continuous monitoring.
- Consumer Empowerment: Consumers can protect themselves by staying informed about recalls, verifying product codes, and practicing general food safety measures. Understanding salmonella’s symptoms and transmission pathways enables individuals to act quickly if they suspect contamination.
Potential Long-Term Implications for Palmer Candy
While a recall can be a significant blow to a company’s reputation and finances, it also presents an opportunity for introspection and improvement. By investing in advanced testing methods, refining supplier audits, and enhancing transparency, Palmer Candy can emerge stronger and more resilient. Should the company handle the recall responsibly, it may maintain consumer loyalty, proving that swift action and honesty can mitigate the worst impacts of a contamination event.
Future of Food Safety
As technology advances, the food industry is poised for a transformation that could significantly reduce the frequency and scope of recalls:
- Predictive Analytics: Using machine learning to forecast contamination risks based on supply chain data, weather patterns, and historical incidents.
- Whole Genome Sequencing: Already in use by agencies like the CDC, this technology rapidly identifies and links bacterial strains, expediting outbreak investigations.
- Blockchain for Traceability: Some companies experiment with blockchain to provide real-time, tamper-proof records of a product’s journey from farm to table. This could make recalls more targeted and less disruptive.
- Enhanced International Collaboration: Given that ingredients often cross borders, multinational agreements and data-sharing platforms can further streamline recall processes.
Consumer Advocacy and Awareness
Public awareness campaigns, social media discussions, and news coverage of recalls like Palmer Candy’s also have a silver lining: they keep food safety in the spotlight. The more people understand about salmonella, cross-contamination, and the intricacies of distribution networks, the less likely they are to fall victim to misinformation or panic. Instead, they can respond with calm, informed actions—checking codes, discarding products, or seeking refunds.
The Road Ahead for Regulators
The FDA, alongside state and local agencies, will continue refining policies and enforcement strategies. If repeated salmonella issues arise in a particular sector—like peanuts or peanut butter—targeted measures might be introduced, such as mandatory pre-distribution testing or stricter facility inspections. These regulatory evolutions, although sometimes burdensome for companies, serve the greater goal of minimizing outbreaks and ensuring public health.
Adapting to E-Commerce
In a rapidly changing retail landscape, e-commerce adds another layer of complexity. Consumers can purchase snacks and candy from websites that ship nationwide, blurring geographic boundaries. Recalls must therefore account for online sales, ensuring that digital retailers promptly remove listings and notify customers. This adaptation requires close collaboration between e-commerce platforms, manufacturers, and regulatory agencies.
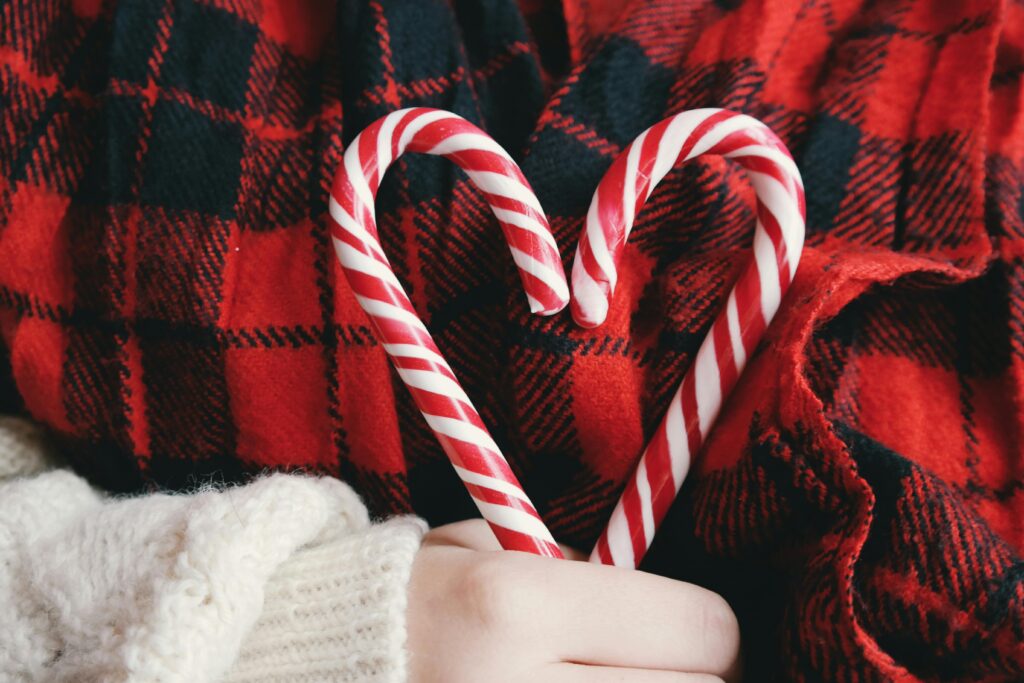
Resilience Through Preparedness
A key lesson from the Palmer Candy recall—and from broader food safety challenges—is the value of preparedness. Companies that invest in robust hazard analyses, advanced testing, and crisis communication plans can respond more swiftly and effectively when issues arise. For consumers, maintaining a basic awareness of foodborne illness risks and recall procedures fosters resilience. When a recall is announced, an informed public can help contain the situation rather than exacerbate it.
Conclusion
The Palmer Candy Company recall, prompted by a potential salmonella risk, underscores the complex interplay of manufacturing processes, regulatory frameworks, and consumer behavior in ensuring food safety. While no recall is ever welcome news, the transparency demonstrated by Palmer Candy and the oversight provided by the FDA highlight how effectively the recall system can work. By acknowledging the inherent challenges, learning from past outbreaks, and embracing continuous improvement, all stakeholders—from farmers and factory workers to regulators and end consumers—can contribute to a safer, more reliable food supply.
As we conclude this deep-dive analysis, it is evident that salmonella contamination, though serious, is neither unstoppable nor unmanageable. Vigilance, science-based policies, and collaborative efforts across the entire supply chain create a robust defense against foodborne pathogens. For Palmer Candy, the path forward involves rigorous corrective measures and ongoing dialogue with the public. For consumers, it serves as a timely reminder that staying informed and proactive can make a tangible difference in preventing illness. Ultimately, the recall process, while disruptive, is a testament to a system designed to protect health and well-being, ensuring that the sweets we enjoy remain a source of delight rather than danger.